This app is from our marketplace
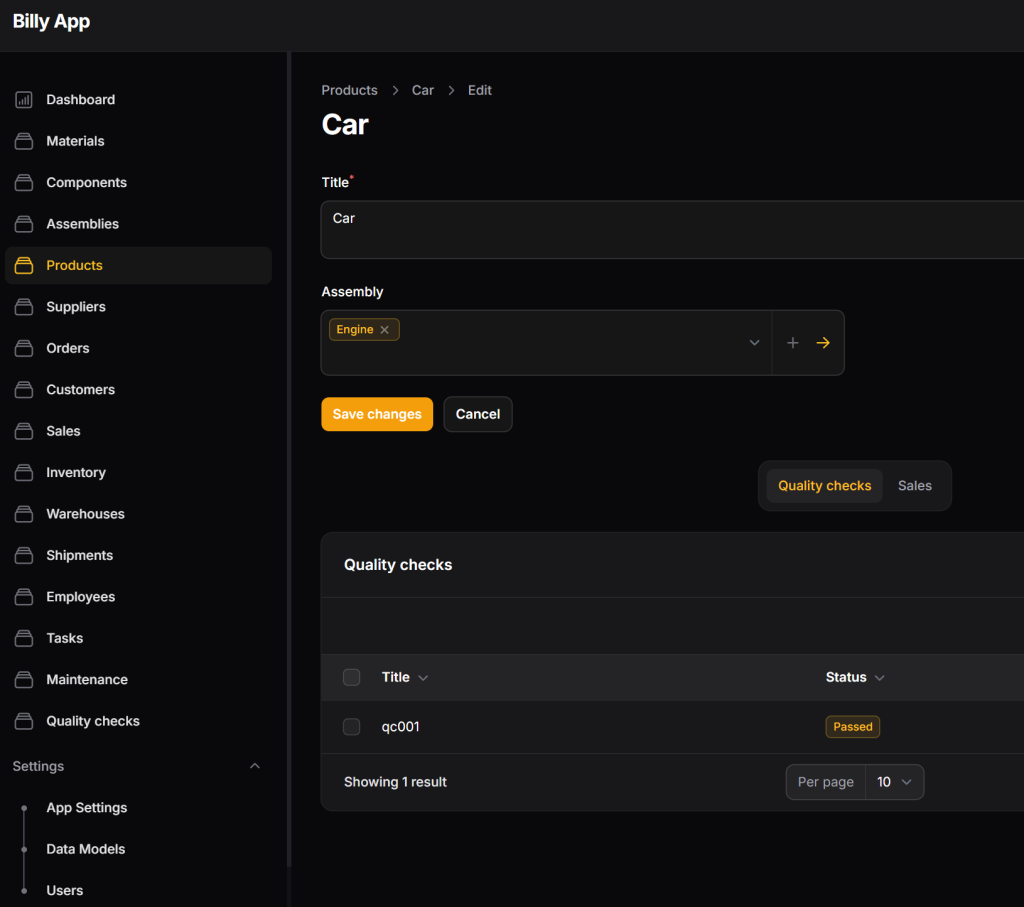
Bill of Materials App
This Bill of Materials (BOM) app offers comprehensive inventory management, streamlined supplier coordination, and automated production tracking, enhancing overall efficiency.
App ensures high-quality control and timely maintenance scheduling, reducing downtime and improving product standards.
streamlined supplier coordination
enhanced overall efficiency
comprehensive inventory management
Solution Benefits
-
Improved Inventory Management:
Track material quantities accurately, reducing overstock and stockouts. For example, knowing the exact amount of steel in inventory helps in planning production runs efficiently.
-
Enhanced Supplier Coordination:
Streamline communication with suppliers through integrated order management. For instance, placing orders for aluminum directly through the platform ensures timely restocking.
-
Cost Reduction:
Optimize material usage and reduce waste. By tracking component usage, businesses can minimize excess material orders, saving costs.
-
Increased Production Efficiency:
Automate assembly tracking and task assignments, leading to faster production cycles. For example, assigning tasks to employees based on real-time data improves workflow.
-
Better Quality Control:
Implement quality checks at various stages to ensure product standards. For instance, regular quality checks on engines can prevent defects and recalls.
-
Enhanced Customer Satisfaction:
Ensure timely delivery and high-quality products, improving customer trust. Accurate sales tracking helps in fulfilling customer orders promptly.
-
Comprehensive Reporting:
Generate detailed reports on inventory, sales, and production for informed decision-making. For example, sales reports can highlight top-selling products and guide marketing strategies.
-
Scalability:
Adapt the platform to growing business needs without significant changes. As the business expands, the platform can handle increased data and transactions.
-
Regulatory Compliance:
Maintain records and documentation to comply with industry regulations. For instance, tracking material sources ensures compliance with environmental standards.
-
Improved Maintenance Scheduling:
Schedule and track maintenance activities to prevent downtime. Regular maintenance checks on assemblies like engines ensure smooth operations.
-
Enhanced Collaboration:
Facilitate better collaboration between departments through shared data. For example, the sales and production teams can coordinate more effectively using the same platform.
-
Data-Driven Decisions:
Leverage data analytics to make strategic business decisions. Analyzing inventory trends can help in optimizing stock levels and reducing costs.